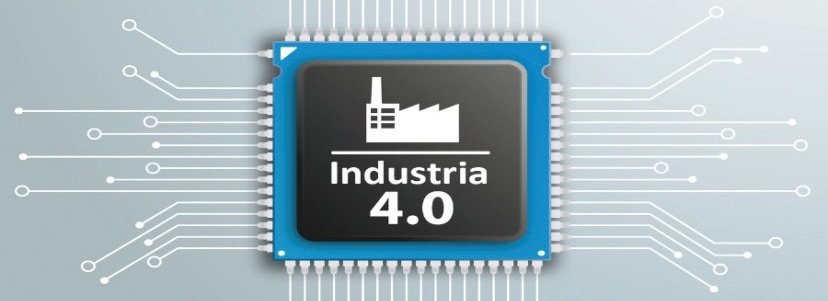
Mantenimiento predictivo en la Industria Española
La industria estima que la identificación temprana y la solución a problemas antes de que ocurran, pueden suponer un ahorro de hasta un 40 por ciento en los costes de mantenimiento.
Fujitsu ha presenta en la sede de Repsol en Madrid, en colaboración con El Observatorio de Industria 4.0, un foro de intercambio de ideas y experiencias y el Club Excelencia en Gestión, una asociación empresarial dedicada a mejorar la gestión y los resultados corporativos, su “Estudio sobre Mantenimiento Predictivo en la Industria 4.0”, algo fundamental para el desarrollo de la fábrica del futuro.
En él, se muestra la importancia para la industria española de implantar proyectos de mantenimiento predictivo, para anticiparse a posibles incidencias o errores activos y mejorar los procesos de producción, a través de diferentes tecnologías como son IoT, IA y la analítica avanzada. Todas ellas imprescindibles para posibilitar la medición, el análisis y monitorización de parámetros que definen los activos y el entorno de la fábrica que nos rodea.
En la industria se estima que la identificación temprana y la solución a problemas antes de que ocurran pueden suponer un ahorro de hasta un 40% en los costes de mantenimiento. Predecir y prevenir fallos o paradas en la infraestructura, controlar los activos o el equipamiento de manera temprana, no sólo asegura una intervención inmediata con la consiguiente reducción de costes, sino que también genera una mayor eficiencia en el negocio de las empresas. Aumentando la productividad de las líneas, optimizando stock, reduciendo el coste de oportunidad, por la no producción y disminuyendo el error humano.
Es importante señalar que el mantenimiento predictivo es valorado como una de las grandes palancas de la digitalización. Pero en líneas generales, el estudio desvela que, al tener muchos años las empresas en nuestro país, les cuesta decidirse a invertir en estos activos, por su maquinaria ya que carecen de procesos de sensorización o porque no guardan sus datos, entre otros aspectos. De ahí, que tan solo, el 35% de la muestra afirme que invierte en nuevas tecnologías. Las cuales se dividen en IoT un 21%, análisis de datos 21% e inteligencia artificial un 12%, quedando en un segundo plano.
El principal motivo de la inversión es optimizar la productividad, pero dejan ver las barreras para lograr la implantación del mantenimiento predictivo como son: el alto grado de inversión, falta de justificación o claro retorno del ROI, así como técnicas. Aunque pese a ellas, el 62,5% recomienda implementar el mantenimiento predictivo para conseguir la competitividad.
Para llegar al Smart Factory se debe entender la transformación digital desde un punto de vista de negocio. Optimizar los stocks y las líneas de producción, alargar la vida útil de la maquinaria y poder hacer un mantenimiento inteligente y programado.
Objetivos del estudio
Tres han sido los objetivos a conseguir en este estudio. Primero, conocer el nivel en el que se encuentran las empresas del sector industrial español. Segundo, exponer los aspectos a tener en cuenta antes, durante y después de abordar un proyecto de mantenimiento predictivo y tercero, compartir las experiencias.
En su desarrollo, realizado del 11 de febrero al 2 de junio de este año, la metodología empleada se ha estructurado en una ficha técnica de ámbito nacional, para contactos tanto clientes de Fujitsu como miembros del Observatorio de la Industria 4.0, que representan, sin lugar a dudas, una muestra amplia del sector industrial español.
Segmentación de empresas objeto del estudio
En cuanto a su tamaño, cabe destacar que en un 57% tienen más de 1.000 empleados. El 28% menos de 500 y el 15% restante entre 500 y 1.000. A todo ello, sumar su facturación. En un 55% de los casos facturan más de 100 millones de euros, el 23% sobre unos 10 millones de euros, y el 17% y el 5% restante de 10 a 50 millones y de 51 a 100, respectivamente.
Y en cuanto a sus cargos consultados. Van desde el Director del Comité de Dirección hasta el Responsable de Ingeniería Industrial, pasando por la Dirección General, Director de Proyectos o de Sistemas, entre otros. Casi todos, el 83% afirma tener activos críticos en sus plantas de producción. De ahí, que el control realizado se hace en un 43% de forma periódica, el 27% en tiempo real y solo el 11% controla sus activos de manera predictiva. Lo cual supone que el 38% de las empresas dedican hasta un 25% del tiempo de sus operarios de planta al mantenimiento y el 18% llegan a emplear hasta la mitad de su horario en estas tareas.
En consecuencia, la inversión desarrollada en mantenimiento predictivo se realiza tan solo en el 27% de las empresas, y eso si llevan tiempo haciéndolo. El 48% de forma reciente. Y del 24% sólo el 6% afirman no tener intención de invertir a corto plazo.
Nuevas tecnologías
La aplicación de las nuevas tecnologías en el mantenimiento predictivo es actualmente del 35% en las empresas industriales españolas. Un 10% indica que ya están empezando a aplicar las nuevas tecnologías en sus procesos de mantenimiento y que llevan algún tiempo haciéndolo. El 28% lo aplicarán a corto plazo y tan solo un 10%, afirman no aplicarlo en un futuro.
Sensorización y análisis de datos
La sensorización de las fábricas pasa por la integración de los dispositivos con los activos y procesos de las líneas de producción, por lo que contar con una sensorización es fundamental a la hora de abordar un proyecto de mantenimiento predictivo. La mayor parte de la muestra afirma contar con este elemento. De hecho, más de la mitad señala que sus activos más críticos están sensorizados con dispositivos de IoT y el 27,6% dice tener la mayoría de sus activos y procesos sensorizados. Sin embargo, tan solo el 10% habla de una sensorizacion total y el otro 10% restante carece de este elemento.
Por otro lado, sólo un 21% afirma tener un histórico de datos como: el historial de paradas, variables como clima, o los recogidos por sus dispositivos, etc…. y por ello, están lejos de aplicar técnicas de análisis sobre ellos. El 30% lo tienen almacenado y accesibles. Pero por norma general, el 36,36% dice que los ha recogido de manera puntual. Y lo más sorprendente, solo el 12% no lo hace.
Elementos motivadores y barreras para invertir en el mantenimiento predictivo
Pese a que tiene múltiples beneficios, para las empresas consultadas los principales motivos que llevan al desarrollo de proyectos de mantenimiento predictivo son: el incremento de productividad, la reducción de costes asociados a un fallo o parada, así como evitar costes añadidos por la no producción. Todos ellos obtienen una puntuación de 3,9 sobre 5. Aunque también se resalta, la importancia de lograr una mejor planificación de las líneas de producción.
En cuanto a las barreras, las principales que se destacan son las técnicas como la falta de sensorización, el bajo grado de madurez de las tecnologías necesarias y todo esto lo ven reflejado como unos elementos que afectan a la seguridad, ciberseguridad, normativa vigente o la propia madurez de los activos actuales. También hay un carácter cultural y estratégico basado en la reticencia ante una falta de retorno claro de la inversión o aversión al riesgo.